The Scientific Research Behind Porosity: A Comprehensive Guide for Welders and Fabricators
Recognizing the complex systems behind porosity in welding is essential for welders and fabricators making every effort for impeccable workmanship. From the structure of the base materials to the ins and outs of the welding process itself, a multitude of variables conspire to either worsen or minimize the presence of porosity.
Recognizing Porosity in Welding
FIRST SENTENCE:
Examination of porosity in welding exposes crucial insights into the honesty and quality of the weld joint. Porosity, identified by the presence of tooth cavities or gaps within the weld metal, is an usual issue in welding procedures. These voids, if not appropriately addressed, can jeopardize the structural honesty and mechanical residential or commercial properties of the weld, causing possible failures in the finished product.

To detect and measure porosity, non-destructive screening approaches such as ultrasonic testing or X-ray inspection are usually employed. These techniques allow for the identification of internal problems without jeopardizing the stability of the weld. By assessing the dimension, form, and circulation of porosity within a weld, welders can make enlightened choices to enhance their welding processes and attain sounder weld joints.

Variables Affecting Porosity Development
The incident of porosity in welding is influenced by a myriad of aspects, varying from gas protecting performance to the complexities of welding criterion settings. Welding criteria, including voltage, existing, travel speed, and electrode kind, also effect porosity development. The welding technique utilized, such as gas steel arc welding (GMAW) or shielded metal arc welding (SMAW), can affect porosity development due to variations in heat distribution and gas coverage - What is Porosity.
Results of Porosity on Weld Top Quality
Porosity formation dramatically compromises the architectural integrity and mechanical properties of welded joints. When porosity exists in a weld, it develops gaps or cavities within the product, reducing the overall stamina of the joint. These gaps work as tension concentration points, making the weld much more at risk to cracking and failure under load. The existence of porosity likewise deteriorates the weld's resistance to deterioration, as the caught air or gases within the voids can react with the surrounding environment, resulting in deterioration gradually. In addition, porosity can prevent the weld's ability to hold up against pressure or effect, additional endangering the general high quality and dependability of the welded structure. In vital applications such as aerospace, vehicle, or architectural buildings, where security and toughness are vital, the damaging impacts of porosity on weld high quality can have serious repercussions, emphasizing the importance of minimizing porosity via correct welding techniques and procedures.
Strategies to Reduce Porosity
To boost the high quality of bonded joints and guarantee architectural stability, welders and makers utilize details strategies targeted at reducing the formation of gaps and cavities within the product during the welding process. One efficient method to lessen porosity is to ensure appropriate product preparation. This includes detailed cleaning of the base metal to get rid of any pollutants such as oil, oil, or dampness that could add to porosity development. In addition, using the proper welding criteria, such as the correct voltage, present, and take a trip rate, is essential in avoiding porosity. Keeping a regular arc length and angle during welding likewise assists lower the likelihood of porosity.

Furthermore, selecting the best protecting gas and preserving appropriate gas flow rates are vital in decreasing porosity. Making use of the ideal welding strategy, such as back-stepping or using a weaving activity, can additionally assist distribute warm evenly and decrease the chances of porosity formation. Ensuring look what i found proper ventilation in the welding setting to remove any possible resources of contamination is important for achieving look at this web-site porosity-free welds. By implementing these methods, welders can successfully reduce porosity and produce high-quality bonded joints.
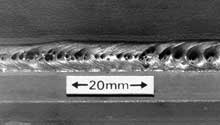
Advanced Solutions for Porosity Control
Applying advanced modern technologies and cutting-edge techniques plays a crucial role in achieving remarkable control over porosity in welding procedures. Additionally, utilizing innovative welding methods such as pulsed MIG welding or modified atmosphere welding can likewise aid minimize porosity issues.
One more sophisticated remedy entails the use of sophisticated welding devices. Using devices with integrated attributes like waveform control and innovative power resources can boost weld top quality and lower porosity threats. The application of automated welding systems with accurate control over parameters can significantly minimize porosity defects.
Furthermore, including sophisticated tracking and evaluation technologies such as real-time X-ray imaging or automated ultrasonic testing can assist in detecting porosity early in the welding procedure, enabling instant rehabilitative activities. Generally, integrating these advanced solutions can substantially enhance porosity control and improve the overall high quality of welded components.
Verdict
In verdict, comprehending the scientific research behind porosity in welding is essential for welders and makers to produce top notch welds - What is Porosity. Advanced services for porosity control can additionally enhance the welding why not find out more process and make certain a strong and dependable weld.
Comments on “What is Porosity in Welding: Vital Tips for Getting Flawless Welds”